Two scientific articles in the Journal of Fluids and Structures outlining the work recently published
This article was originally published on Sept. 7, 2022
There aren’t many valve companies in the world that have the honour of saying they have published peer-reviewed articles in scientific journals.
Following a joint industry-academia collaborative study, however, Master Flo can now say it’s one of them.
The study, prompted by inexplicable choke trim collapses in control valves that were in service in high-rate gas flow applications offshore, has produced some promising insights.
“The results revealed flow phenomena we were not previously aware of and represent an advancement of knowledge in this field, and science in general,” says Master Flo USA General Manager Frank Koeck, one of the authors of the study.
For Koeck, the problem investigated by the study and students at the helm of it, has perplexed him ever since he first encountered it.
“I saw this early in my career 25 years ago, inexplicable failures of a similar nature, similar geometry, similar size valve, and similar flow rates,” notes Koeck. “25 years ago, the ability to analyze (the problem) was limited. We could only take it so far, only do empirical measurements and guess at the causes from the actual measurements that were taken.”
But things sure have come a long way in the past two and a half decades. Computing power especially.
The analysis that was conducted through the course of the study was done using the University of Houston’s supercomputing cluster. For one of the articles, which examined incompressible flow through a choke valve, each simulation thereof that was run through the cluster took seven hours. Were the simulation to be executed on a standalone CPU, it would have taken 49 days.
For the second article, a study on compressible flow through a choke valve, the simulations were much more demanding.
Each one took more than 50 days on the cluster, equivalent to 8554 days of single CPU time.
Once the analysis was done, Koeck says it was time for them to validate the results.
“We designed and built a full-scale acrylic model and observed the flow through Particle Image Velocimetry (PIV),” he says. “This consisted of ‘seeding’ the flow with nearly weightless particles that would remain in suspension while flowing. A laser illuminated these particles as they flowed through the model, and a high-speed camera captured pictures at a rate of 400 frames per second.”
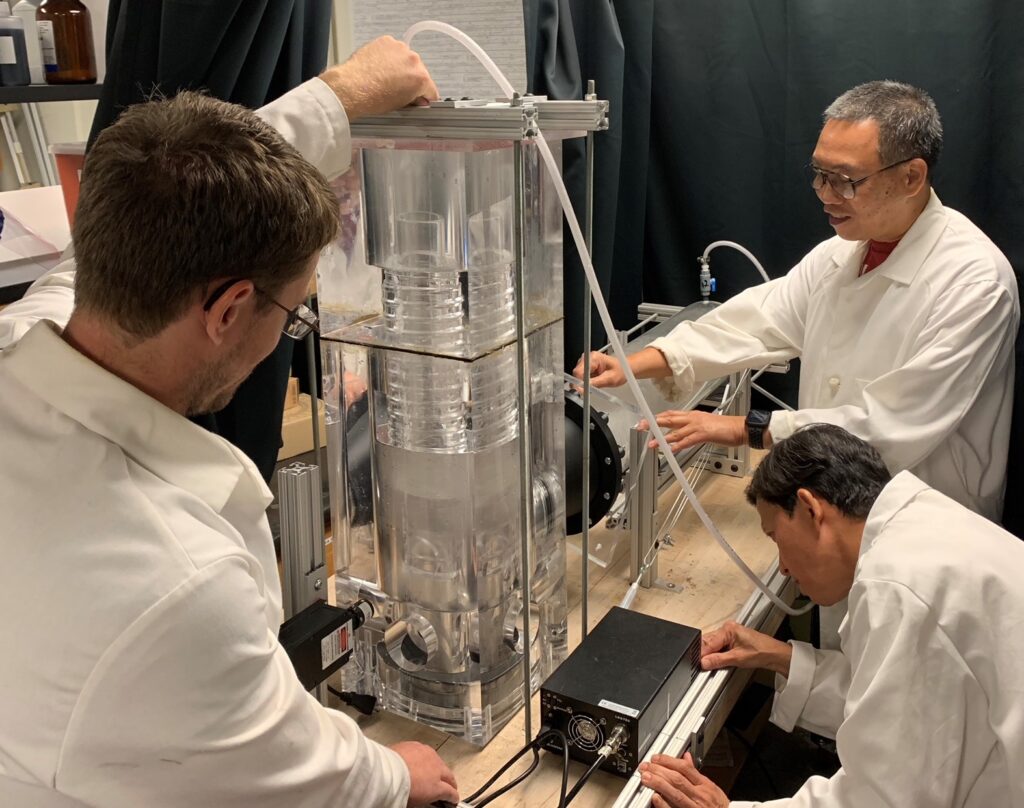
Study co-author Trever Gabel sets up the experimental acrylic model provided by Master Flo.
The resulting videos from the high-speed camera provided the validation Koeck and the research team needed in order to get their articles published, and advance current choke knowledge to a new level.
Leading the research team was engineering master’s student Harsa Mitra from the University of Houston, who was put on the Master Flo payroll as he completed his thesis statement on the question at hand. Helping guide him through the study were two principal investigators, fluid dynamics expert Dr. Kamran Alba and numerical analysis expert Dr. Rodolfo Ostilla Mónico. Undergrad student Trevor Gabel, along with Master Flo USA Engineering Manager Dan Williams, rounded out the remaining authors.
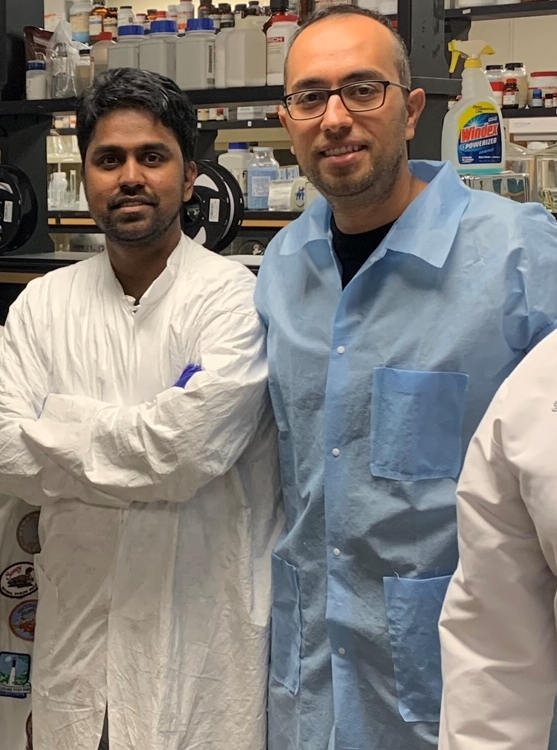
Lead researcher Harsa Mitra, left, and fluid dynamics expert Dr. Kamran Alba.
“I’m very pleased with the work they did and proud of our students,” said Koeck. “We provided the funding, which was not inconsequential, and designed both the analytical and physical test models, and helped edit the reports. But the actual numerical analysis was conducted by Mitra and the rest of the team. It was generous of them to put (Dan and I) as co-authors on this.”
Interestingly enough, the inexplicable problem, at least as it relates to choke trim failure, had already been solved by Williams and the engineering team. They designed a Multi-Port, Multi-Metal trim that has so far not seen any subsequent failures in this specific high-rate gas offshore application.
Pursuing why it happened, though, remained an important scientific — and business — pursuit.
“We didn’t have to do this,” says Koeck. “It’s an opportunity to make something better and bigger, to take advantage of the situation that created this opportunity. We didn’t have to do the analysis, but we can do the analysis, and it will be viewed by our customer as a proactive measure that we took of our own initiative to demonstrate we are the experts at what we do.
“We are at the forefront of technology in our field and understanding what actually goes on, not just the mechanical engineering of it — it’s not just dumb metal — it’s understanding the flow dynamics around the product we produce.”
So, is a super choke in the offing? Not necessarily, says Koeck, though a different choke design and possibly materials used within it may be beneficial to pursue when it comes to offshore high-rate gas applications.
“That is our recommendation coming out of this investigation,” concluded Koeck. “We can certainly infer the dos and do nots, design-wise, from this study.”